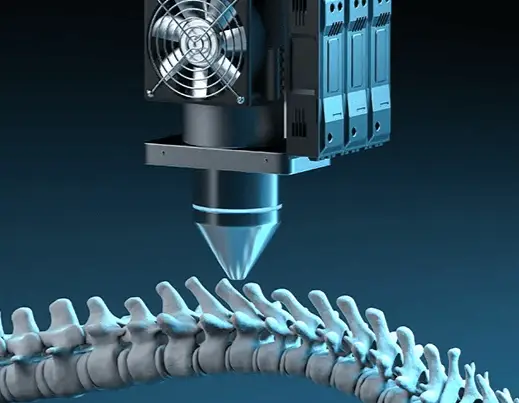
Three-dimensional (3D) printing is revolutionizing medical care, shifting the focus from mass-produced solutions to patient-specific treatments. This innovative technology enables the creation of custom prosthetic hands for children, crafted from lightweight materials with adaptable control systems. These continuous advancements highlight how 3D-printed prosthetics are becoming more affordable and accessible. The success of personalized prosthetics demonstrates the power of 3D printing, where a digital design is transformed into a physical object, built layer by layer.
The capability of 3D printing to create precisely shaped objects across various materials has led to innovations such as custom replacement joints and multi-drug pills with exact dosages.
Better Body Parts
The use of 3D printing in healthcare began in the 1980s with techniques like stereolithography, which used lasers to solidify liquid materials into 3D forms. The medical field quickly recognized its potential for personalized implants and prosthetics. Early applications included tissue scaffolds to support cell growth, with researchers at Boston Children’s Hospital even creating durable replacement bladders using patient cells.
As the technology progressed, bioprinting emerged, utilizing living cells to construct anatomical structures. In 2013, Organovo successfully produced the first 3D-bioprinted liver tissue, opening doors for organ transplantation. While creating full, functional organs for transplant remains experimental, current research focuses on developing smaller tissues and refining techniques for better cell viability.
3D printing has already transformed prosthetics, enabling the production of affordable, custom-fit devices that perfectly suit patients and can be easily replaced as children grow. Similarly, 3D-printed implants like hip and spine replacements offer a more precise fit than traditional, standard-sized options, improving integration with the body. Custom titanium facial implants and skull replacements have also been successfully used. Dentistry has seen significant advances, with companies like Invisalign using 3D printing for custom-fit aligners. Scientists are also exploring novel materials like self-healing bioglass for cartilage repair and developing 4D printing for adaptive medical devices, such as stents that adjust to blood flow changes.
Simulating Surgeries
3D-printed anatomical models are invaluable tools for surgeons, allowing them to understand complex cases and enhance surgical outcomes. Created from medical scans (X-rays, CTs), these models enable surgeons to practice procedures beforehand. For instance, a 3D-printed heart model allows for the simulation of complex surgeries, potentially leading to shorter operating times, fewer complications, and reduced costs.
Personalized Pharmaceuticals
In the pharmaceutical sector, 3D printing allows for personalized drug dosages and delivery systems. The precise layering of components ensures medications contain the exact dose for each patient, exemplified by the FDA-approved anti-epileptic drug, Spritam, in 2015. This technology is moving drug production beyond factories into community pharmacies and hospitals, facilitating on-site medicine creation tailored to individual patient needs. However, regulations for 3D-printed drugs are still evolving, with concerns about ingredient stability post-printing, the need for clear production guidelines, and comprehensive training for pharmacists.
Printing for the Future
Despite rapid advancements, significant challenges and opportunities persist in 3D printing for healthcare. Ensuring the quality and safety of 3D-printed medical products, along with addressing affordability and accessibility, remain crucial. Long-term safety concerns regarding implant materials, including biocompatibility and nanoparticle release, require rigorous testing. High initial investment and a lack of standardized workflows can limit widespread adoption, especially in underserved areas.
On a promising note, artificial intelligence (AI) is expected to be vital in developing improved 3D-printed medical products. AI algorithms can analyze patient data to optimize design and fabrication, for instance, using AI-driven image analysis to create accurate 3D models for customized implants. Furthermore, machine learning can predict long-term performance and potential failure points of prosthetics, enhancing durability and patient safety.
3D printing continues to push boundaries, even within the human body. Researchers are exploring techniques to turn injected liquids into 3D gels using ultrasound, potentially for drug delivery or tissue replacement. Ultimately, the field is rapidly progressing towards highly personalized treatment plans, precisely adapted to each patient’s unique needs, thanks to the precision and flexibility of 3D printing.